Articolo pubblicato su Sistema Serramento giugno 2023
La prima parte dell’incontro del 16 novembre 2022 in Working Process, a Rivergaro in provincia di Piacenza, lo abbiamo riportato nello scorso numero di Sistema Serramento e lo riprendiamo brevemente in questa seconda parte. Il Diario di viaggio del “dietro le quinte” di questa straordinaria realtà è iniziato intorno alla ‘tavola rotonda’ con Stefano Schegginetti, Filippo Schegginetti e Paolo Perservati ed è proseguito con la visita all’ufficio Project Management. In questa seconda parte riportiamo il pranzo con i personaggi del settore fra Working Process, la Falegnameria Cobola e PM serramenti e l’incontro nel reparto produttivo con il titolare di PM serramenti Patrizio Pesenti che ha acquistato il nuovo centro di lavoro Logos Life Evo 3555. Significativa la visita al reparto produttivo con il Responsabile di Produzione Valentino Maccagni, e infine l’incontro con l’ingegner Fabio Marchesi per l’aspetto certificativo che restituiscono nell’insieme un mosaico valoriale distintivo. Attraverso la costante evoluzione dello schema produttivo delle 7P “Prefinito, Prefresato, Presquadrato, Pronto, Perfezione, Profitto, Performances” e la filosofia TWC “Technology Without Compromises” l’azienda ha coinvolto i migliori specialisti e influencer del settore. Proseguiremo con altri incontri per immergerci nel mondo amministrativo, finanziario e commerciale dell’azienda.
Come è emerso durante la tavola rotonda del 16 novembre 2022 presso Working Process, a Rivergaro in provincia di Piacenza – nella prima parte pubblicata su Sistema Serramento n° 39/2022 –, si tratta di una realtà importante che cresce giorno dopo giorno, una di quelle aziende che si è ingrandita costantemente nel tempo con l’obiettivo di una crescita direttamente proporzionale in termini di qualità. Lo scopo di questo “diario di viaggio all’interno di Working Process” è proprio quello di raccontare le strategie di pensiero che precedono quelle concrete e per questo i nostri incontri prevedono diversi itinerari all’interno dell’azienda, volti a incontrare i personaggi che stanno dietro le quinte dell’azienda, i tecnici che lavorano gli ingredienti per creare dei prodotti distintivi! Il processo che si è evidenziato è inverso, se la forma della finestra “normalmente” segue il macchinario, in Working Process questo concetto è stato invertito perché deve essere la macchina che segue la forma del serramento. Attraverso la costante evoluzione dello schema produttivo delle 7P “Prefinito, Prefresato, Presquadrato, Pronto, Perfezione, Profitto, Performances” e la filosofia TWC “Technology Without Compromises” l’azienda ha coinvolto i migliori specialisti e influencer del settore. «È il coraggio che dà origine alla nostra filosofia TWC – sottolinea Paolo Perservati – , che ha portato Working Process a superare i limiti convenzionali delle macchine, grazie al coinvolgimento di tutte le persone che lavorano in azienda e tutti i partners esterni dell’intera filiera». Il progetto non parte dal momento in cui viene chiuso il contratto e viene scelta la marca dell’utensile ma molto prima per sviluppare i cicli di lavoro e di produttività ad hoc sulla finestra del cliente. Va evidenziato che non producendo l’azienda impianti standard per quantificare il tempo necessario per realizzarli è necessario avere un approccio analitico per prevederlo esattamente ed essere precisi in questa modalità operativa è di estrema importanza. Nella prima parte di questo incontro è emerso anche che vengono affrontati impianti sempre più articolati con macchine e software di terzi e con molta automazione di processo e che sono sempre più importanti i controlli dei tempi di attraversamento e di installazione in azienda: la fase cruciale. In Working Process la struttura stessa dell’offerta è caratterizzata da una proposta di servizi molto più ricca rispetto quella relativa alla macchina in sé (ad esempio, la realizzazione customizzata del layout e dello studio del processo produttivo, l’ispezione e controllo degli spazi e dei vincoli tecnici presso la sede del cliente, la strategia e il controllo delle cicliche di lavorazione dei prodotti principali, in collaborazione con il produttore utensili e software house scelti dal cliente).
Nella prima parte abbiamo riportato la profondità che l’azienda conferisce alla pianificazione potendo contare su risorse finanziarie che permettono di acquistare materiale in anticipo e di avere la possibilità di disporre in tempo reale dei componenti da montare. All’ufficio acquisti c’è personale dedicato che effettua acquisti on line in tutto il mondo e questo permette di bypassare le inefficienze e la speculazione dei canali consueti.
Una strategia che ha permesso a questa realtà di mantenere le consegne e di non rinunciare a nessun ordine in un contesto di trasparenza e collaborazione.
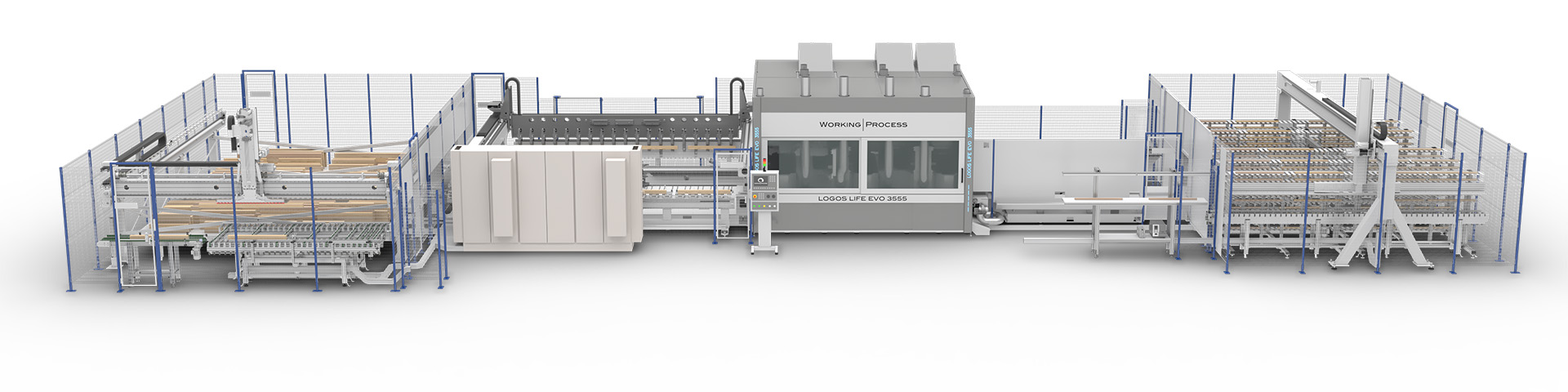
IL PRANZO INTORNO AL LEGNO
Durante il pranzo in un’elegante sala dedicata, con un unico grande tavolo quadrato, la forte personalità di Patrizio Pesenti rallegra la tavolata. La sua poi, è una storia da raccontare – e lo faremo – anche perché rappresenta la vittoria di una grande battaglia, prima umana che professionale. Certo quella imprenditoriale mira a una qualità eccelsa. Cobola Falegnameria rappresentata da Corrado Cobola e due suoi collaboratori non ha bisogno di presentazioni, identificando una antica e nota realtà sul suo territorio e sul nostro Stivale.
Poi c’è l’autorevole rappresentanza di Working Process che ha ospitato tutti noi, con Filippo e Stefano Schegginetti e Paolo Perservati, maestro di queste alchimie in cui si fondono competenze professionali e filosofie di pensiero e umane fra persone affini che arricchiscono sempre un po’ tutti. Inevitabile in una tavola costituita da otto commensali che appartengono da sempre al settore del legno, la sua valorizzazione: «I falegnami non hanno paura del PVC – afferma perentorio Patrizio Pesenti –, hanno un altro mercato. Il PVC non crescerà ulteriormente: i numeri dicono questo. E poi, ci sono cose che il PVC non può fare».
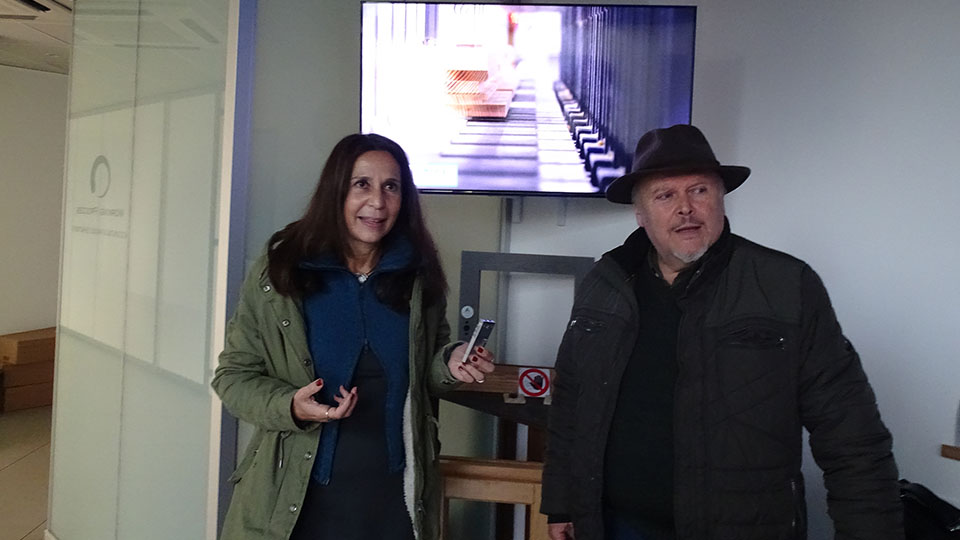
IL NUOVO LOGOS LIFE DI PM SERRAMENTI
Dopo il pranzo ci ritroviamo intorno alla nuova Logos di Patrizio Pesenti che, con il suo sguardo vivace fisso sulla macchina in funzione, parla con Corrado Cobola, Paolo Perservati, Stefano Schegginetti, oltre al suo collaboratore Joseph e al tecnico di Working Process Florian Gargiulo.
Il centro di lavoro LOGOS LIFE EVO 3555 dotato di magazzino intelligente IMML e scarico SB fa bella mostra di sé nello spazio produttivo di Working Process, è l’ultimo gioiello di PM serramenti dopo le altre LOGOS acquistate in precedenza (Logos IWC e Logos SCH). L’imprenditore non ha dubbi: le tecnologie di Working Process rappresentano il primo passo nel futuro!
«Questa è la fase di preparazione per i test di accettazione – spiega Paolo Perservati –, in questa fase sono coinvolti oltre al cliente, gli utensilieri e le software house esterne. Assistere a tutte le fasi di preparazione al test di accettazione è importante perché in questo arco temporale vengono simulate tutte le casistiche prima che la macchina venga installata presso il cliente. Sono impianti complessi (non complicati) che hanno bisogno di una conoscenza profonda per poter essere sfruttati al meglio».
Chiediamo a Joseph, che nonostante la sua origine senegalese ormai parla quasi il bergamasco, se sia importante questa esperienza.
«Questo lavoro è molto importante – risponde Joseph –, perché ti fa crescere molto bene».
«Si tratta di una macchina costruita su misura per le esigenze del cliente – aggiunge Florian Gargiulo –, partendo dalle dimensioni del capannone, dal tipo di finestra e dai volumi di produzione di PM Serramenti».
«Questo è il terzo impianto che acquistiamo da Working Process – spiega il titolare di PM serramenti Patrizio Pesenti –. I primi due erano abbastanza simili, questo terzo è un impianto decisamente diverso grazie al magazzino intelligente di carico. La Working Process è la numero uno, conosco Massimo Schiavetta dal 1993, lui ha creato il primo sistema con ritorno pezzi di Sac Sueri e mi ha ha presentato nel 1996 la Sapiens: il primo centro di lavoro nato sotto il marchio di Working Process».
La vocazione di PM serramenti per la natura viene trasmessa fin dall’home page del sito suddiviso nelle tre sezioni: azienda, natura, progetti. Produrre serramenti che ripropongono le architetture tradizionali di un tempo e interpretano le tendenze del design contemporaneo, con la dedizione di ogni persona alle proprie mansioni, guidate dalla paziente maestria del sapere fare artigiano e dal ritmo serrato tra i reparti è il fine di questa realtà bergamasca.
«Dal 1984, l’azienda plasma la materia di più tipi di legno – afferma Patrizio Pesenti – e di ognuno esalta la tipica bellezza, sposa il naturale design, ne diffonde le inconfondibili note profumate, quelle del Castagno, del Cedro, del Ciliegio e del Douglas, i materiali che utilizziamo. Le realizzazioni spaziano da Cernobbio ai Caraibi, ma anche per edilizia civile più modesta. Cerchiamo di essere un passo avanti e di non subire il mercato, anticipando le mode. Tutti i nostri serramenti esprimono la qualità dei materiali selezionati e della tecnologia studiata da designer e architetti che si riflette nell’originalità dei progetti attraverso la personalizzazione del design, delle forme e delle misure. Il bravo architetto deve confrontarsi con il professionista, creare il feeling con il falegname e trovare il giusto mix. La continua ricerca e innovazione di prodotto ci ha portato anche ad alcuni brevetti. Abbiamo un brevetto di utilità per degli scuri orientabili, ideale per i Caraibi. Un altro brevetto per porta con apertura a scomparsa del telaio e un brevetto di un serramento di 28 centimetri anche sul nodo centrale tenuto insieme dal vetro. Realizzare infissi che portano impressi i tratti somatici tipici del legno e i principi di ecosostenibilità diffusi negli spazi dove verranno installati come uffici, ville, chiese, residenze, chiostri, teatri rappresenta il nostro lavoro quotidiano. Farlo con l’esperienza di 40 anni di storia che guardano al futuro la nostra forza».
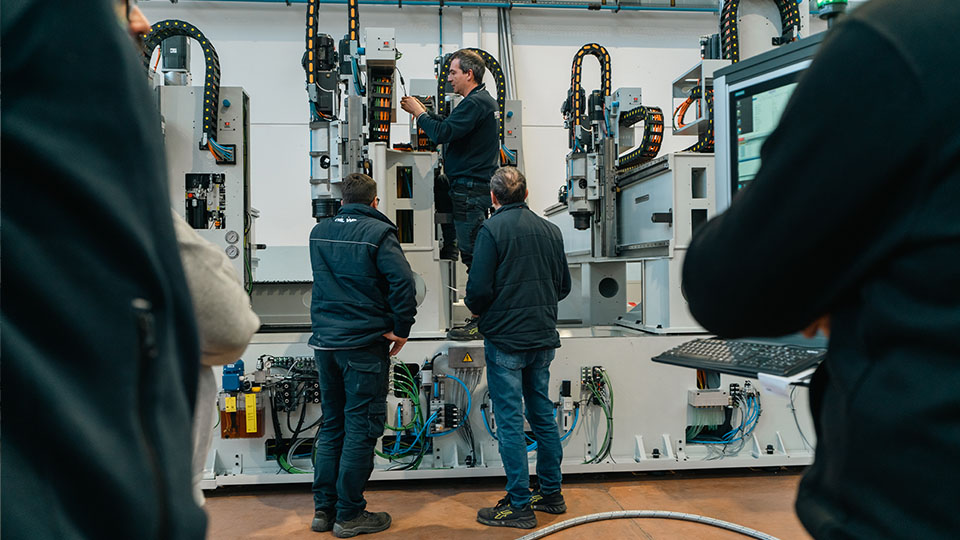
IL REPARTO PRODUTTIVO
Incontriamo poi il responsabile del reparto produttivo di Working Process Valentino Maccagni, in un percorso restituito da Paolo Perservati che ci illustra il collegamento che avviene con l’ufficio tecnico meccanico e software di Working Process, l’efficacia della comunicazione tra le Aree Tecniche dell’Azienda e dell’ulteriore analisi alla quale viene sottoposta la commessa.
Valentino Maccagni è il responsabile della produzione e di officina – introduce Paolo Perservati –.
Quindi seguite tutte le macchine a livello di pianificazione e realizzazione?
«Abbiamo un capo commessa con un team dedicato al quale viene affidato il montaggio dell’impianto e viene attribuita una pianificazione di avanzamento delle varie fasi costruttive. Autonomamente vengono individuate le fasi di montaggio attraverso un visualizzatore 3D di Catia5, il nostro software Dassault Systemes di progettazione meccanica – risponde Valentino Maccagni –. Noi ci occupiamo dell’assemblaggio delle parti meccaniche, sia in linea che nel reparto di premontaggio. Ogni macchina ha delle particolarità specialmente per quanto le customizzazioni a livello di movimentazione/automazione».
Il fatto che sia cresciuta la parte software che cosa ha significato per la parte meccanica?
«Anche la parte meccanica – commenta ancora Valentino Vaccagni – si è evoluta di pari passo».
«L’evoluzione viene dettata dalla parte software – aggiunge Paolo Perservati –, però di pari passo viene supportata da quella meccanica».
«Proprio perché produciamo per commessa – spiega Paolo Perservati –, qui ci sono aspetti produttivi un po’ diversi rispetto a quelli di altre aziende, e anche la gestione della costruzione della macchina è concepita in quel senso. Abbiamo addetti al montaggio che sono completamente trasversali: chi prende all’inizio una commessa la porta fino alla fine».
Devono avere competenza di tutti gli elementi di cui si compone la macchina!
«I montatori meccanici hanno competenza anche del reparto di premontaggio – osserva Paolo Perservati – che monta tutti i componenti in aggregati più complessi prima ancora che vengano installati nelle macchine, previa approvazione. Come dice Valentino la flessibilità deriva anche da questo approccio di costruzione della macchina. Ovviamente a monte ci deve essere una gestione di tempistiche e di ordinativi che loro siano in grado di recepire. Per questo la produzione è direttamente coinvolta già dall’inizio. Addirittura in modalità previsionale».
Quando tempo serve mediamente per realizzare una macchina?
«Per quanto riguarda solo il montaggio meccanico andiamo dai due ai quattro mesi – risponde Valentino Maccagni –, di più per macchine grandi. Ovviamente ci sono altre fasi a monte e a valle che possono portare il tempo di attraversamento fino a 16 mesi per le linee di grandi dimensioni».
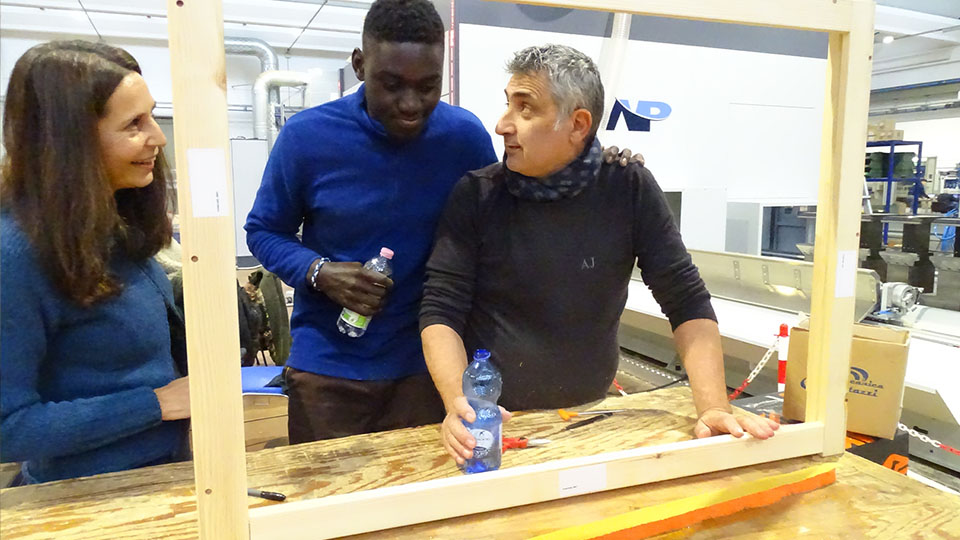
L’ASPETTO CERTIFICATIVO
Infine ritroviamo Stefano Schegginetti che ci presenta l’ingegner Fabio Marchesi, responsabile dell’aspetto certificativo sin dagli esordi di Working Process. Ci troviamo all’ingresso, spazio che accoglie gli ospiti con l’esposizione di angoli minimali e un video che racconta la trasformazione produttiva di tante realtà artigianali del settore legno, come evidenzia Paolo Perservati.
«In questo momento stiamo affinando delle cose che, magari, non sono ancora adottabili al 100% nel nostro settore – commenta Stefano Schegginetti – e nemmeno per noi si possono definire raggiunte al 100%, e comunque il cammino sarà ancora di qualche anno considerando anche le contingenze, io però già vedo che gradualmente, perseverando, ci arriveremo! Il nostro obiettivo fondamentale è quello di percorrere questo cammino, pur accettando di non aver realizzato il massimo della economicità e del ritorno di quello che stiamo facendo, considerandolo un investimento sul campo, spendendo queste risorse sul prezzo della macchina. Quando arriveremo a questo punto, questa sarà un’azienda ben strutturata con una superficie di 38.600 metri quadrati che già stiamo urbanizzando. Affrontando anche le strette che però vanno nella direzione giusta. C’è una spinta continua all’innovazione che rappresenta la linfa del nostro organismo aziendale».
Il profilo del minimale esposto nella sala d’ingresso lo conferma perché ha superato anche il problema del nodo centrale! E sul finire incontriamo anche un certificatore di lungo corso, Fabio Marchesi: un testimone importante della crescita di Working Process.
«Dal 1998/99 ho visto nascere le prime macchine Sapiens – esordisce l’ingegner Fabio Marchesi –. Qui c’è stata un’intuizione geniale, quella di ispirarsi alle macchine per il ferro, Piacenza è un distretto mondiale in questo senso, e dà lì è partito tutto, puntando sull’automazione e sulla qualità. Il loro successo dimostra come hanno visto giusto».
I primissimi impulsi sono stati dati da Massimo Schiavetta.
«Nel lontano 2000 parlavamo già di nastri, di sistemi, di robot – conferma Fabio Marchesi –, il mercato non era pronto ma lo è stato dopo. La prima macchina è stata montata in un piccolo capannone, io ero lì per la direttiva macchine, per certificare».
«C’è stato un grande sviluppo – aggiunge Fabio Marchesi – anche dal punto di vista ingegneristico».
«Grazie anche ai tecnici e ai progettisti – commenta Stefano Schegginetti – che hanno avuto spazio giustificato dalle loro grandi capacità».
Come possiamo sintetizzare in pochi concetti l’evoluzione di Working Process?
«Siamo partiti da quello che inizialmente poteva essere un buon artigiano – risponde Fabio Marchesi – per arrivare a un’azienda industriale, anche nello sviluppo progettuale delle macchine dal punto di vista della sicurezza, della resistenza, dell’affidabilità delle macchine. Nel 2000 la movimentazione automatica delle macchine non si sapeva nemmeno cosa fosse, si andava per tentativi, spesso con delle applicazioni pratiche che non funzionavano, oggi si vedono delle macchine che, tra l’altro, sono anche belle da vedere, non solo funzionali, silenziose, sicure. Consideriamo che dal 1990 al 2000 trovare un programmatore di macchine utensili era un problema, oggi si lavora su macchine semplici».
«Si tratta di macchine complesse – sottolinea Paolo Perservati – che però devono a maggior ragione essere user friendly, ci sono sistemi guidati di autoapprendimento e sicurezza di grande efficacia».
«Con vantaggi enormi – precisa ancora l’ingegner Marchesi – dal punto di vista della precisione, oggi sempre più richiesti».
«L’ingegnere ha visto nascere l’azienda – conclude Stefano Schegginetti – e ha dato dei consigli preziosi. Questo si completa con un senso di appartenenza da parte di tutti».
di Sonia Maritan e Pietro Ferrari