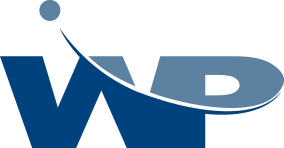
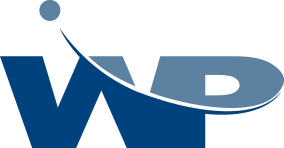
Logos Life EVO XS
Il massimo della produzione di finestre in legno con il minimo ingombro!
Centro di lavoro compatto completamente automatico per la produzione di finestre e porte in legno di qualsiasi forma e dimensione. È dotato di carico e scarico automatici, manipolatore a doppia presa, struttura monoblocco con 2 o 3 mandrini per la fresatura. Dispone di 8 pinze portapezzo completamente indipendenti e 128 posti utensile che garantiscono la massima flessibilità e produttività. È integrabile con i magazzini intelligenti per il carico e lo scarico.
Ideale per una produzione da 10 a 25 finestre al giorno!
Sistema di Carico
Sistema di carico BB e IMML ottimizzato per il carico di file di pezzi, la massimizzazione dello spazio disponibile e il posizionamento variabile dei pezzi.
Questo sistema completamente automatizzato è in grado di caricare contemporaneamente da 1 a 10 pezzi, gestendo il loro bloccaggio ottimale nelle pinze e consentendo la lavorazione su tutte e 6 le facce. Inoltre, offre la verifica dimensionale degli elementi in ingresso, l’ottimizzazione della disposizione dei pezzi in fila, la preparazione del carico e la gestione di pezzi con larghezze differenti.
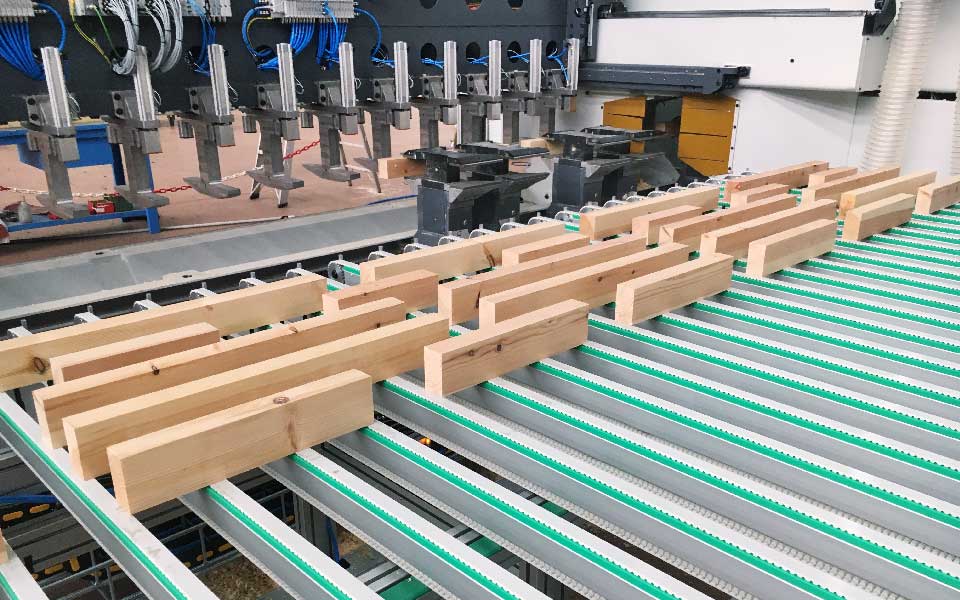
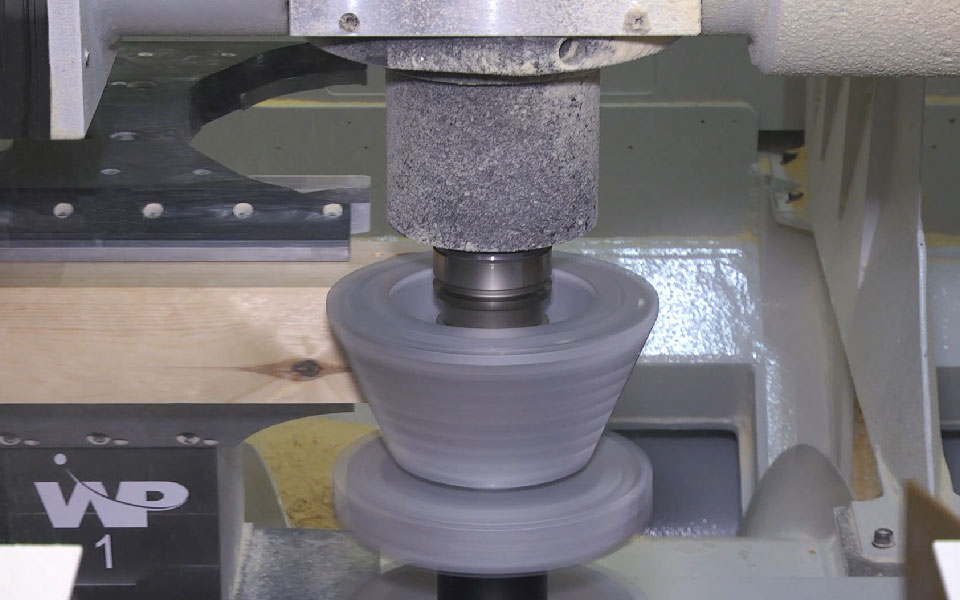
Pinze da Trasporto
Le pinze doppie di bloccaggio pezzo sono progettate con chiusura pneumatica e traslazione longitudinale motorizzata indipendente. La loro dimensione e forma sono state ottimizzate per garantire la migliore accessibilità degli utensili al pezzo durante la lavorazione.
Queste pinze sono gestite come assi indipendenti di interpolazione, offrendo così una flessibilità aggiuntiva che si traduce in un aumento della capacità produttiva complessiva. Le pinze sono caratterizzate dalla flessibilità, dalla robustezza e dall’adattabilità, con una regolazione della pressione in base alle specifiche esigenze di lavorazione e un posizionamento ottimale su legno per garantire una presa efficace e di alta qualità.
Ogni pinza è progettata per essere indipendente, con la possibilità di regolare la pressione di presa, riposizionarla all’infinito senza compromettere la precisione. Inoltre, sono dotate di caratteristiche adattabili, come microaghi, per affrontare diverse fasi di lavoro e anticipare eventuali future lavorazioni.
Manipolatore
Il manipolatore con struttura a portale sfrutta la gestione elettronica della profondità e dell’altezza per la movimentazione dei pezzi in impianto.
Il corretto dimensionamento della struttura e l’impiego di motorizzazioni Gantry consentono elevate precisioni di riposizionamento, estrema rigidità ed elevate velocità di movimentazione.

Teste Operatrici
Le teste operatrici T1, T5 e TBR rappresentano il risultato di 20 anni di ricerca e sviluppo. Ad esempio, i sistemi di doppio bloccaggio laterale delle teste T5, anche con asse C integrato, offrono flessibilità e precisione nel posizionamento degli utensili.
Ciò assicura condizioni ottimali di “taglio” riducendo lo stress sull’elettromandrino.
Magazzino Utensili
Il Magazzino Utensili è concepito come sistema a rastrelliera RACK con struttura in acciaio elettrosaldato e con movimento a scorrimento longitudinale su guide con pattini a ricircolo di sfere.
Il sistema consente di effettuare le operazioni di cambio utensile simultaneamente su tutti i mandrini, riducendo i tempi passivi ed aumentando di conseguenza la produttività.
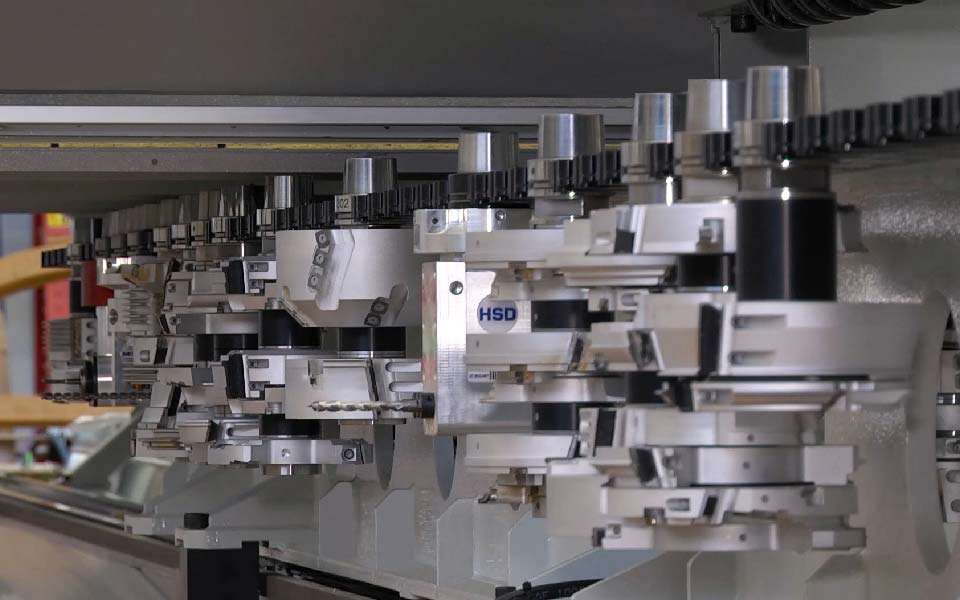
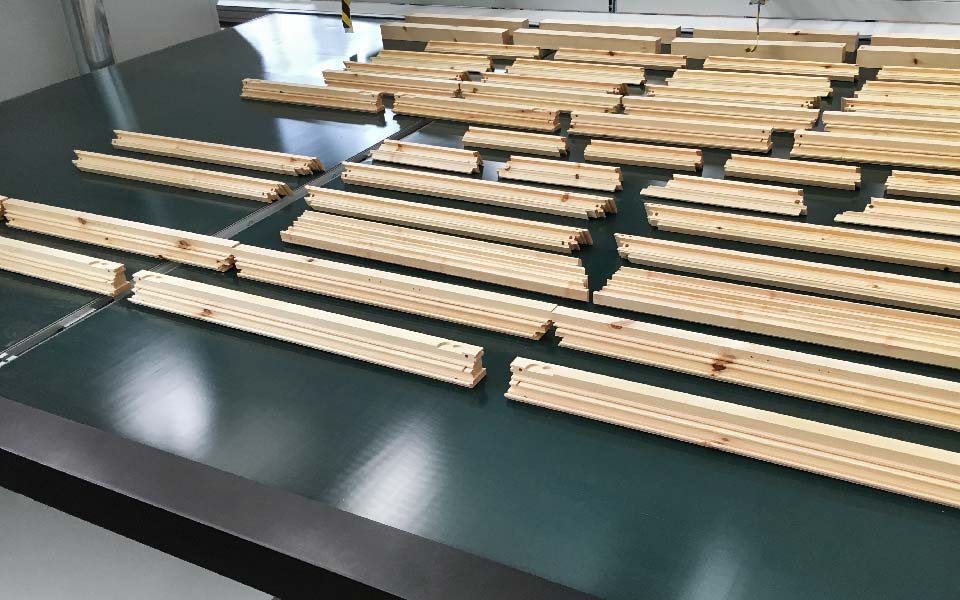
Sistema di Scarico
Il sistema di scarico proposto è altamente personalizzabile e modulare, progettato per garantire un’efficienza ottimale nel processo di gestione della logistica. La sua capacità di rispettare una sequenza di lavoro predefinita assicura una sincronizzazione accurata durante il processo di scarico, garantendo un flusso di lavoro impeccabile e un utilizzo ottimale delle risorse.
Un punto forte di questo sistema è la sua autonomia operativa estesa, che varia da un minimo di 1 ora fino a 3 turni continuativi (UML). Questa caratteristica offre una flessibilità operativa notevole, riducendo al minimo i tempi di inattività e consentendo una gestione continua delle operazioni.
Il sistema esegue in modo efficiente le operazioni di scarico, inclusi avanzati controlli di qualità per garantire la conformità agli standard. Inoltre, integra un processo automatico di etichettatura al termine delle operazioni di scarico, semplificando la gestione dei materiali e migliorando la tracciabilità.
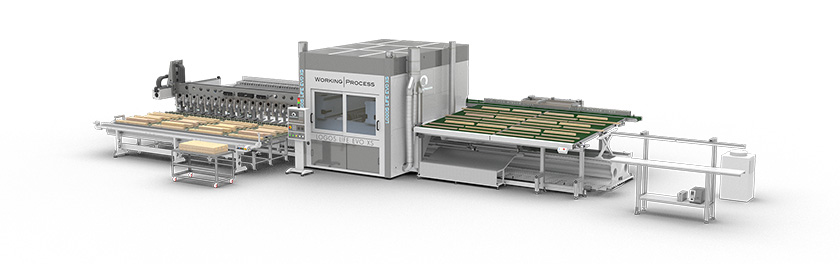
Logos Life EvO XS: 2253 BB SB
Linea di produzione per finestre CNC multi-mandrino con caricamento manuale del pezzo e scarico automatico, 2 portali con 2 mandrini di fresatura, 8/10 morse completamente indipendenti e 160 posti utensile, garantendo massima flessibilità e produttività.
• 2 motori mandrino T5/T5c
• 8/10 morse indipendenti
• 160 posti utensile
• Sistema di pulizia del porta utensili
• 1 operatore richiesto
• Scarico SB (Scarico Bancale)
• IMML (opzionale)
• Spazio 16,4 metri x 7,5 metri
• 2 motori mandrino T5/T5c
• 8/10 morse indipendenti
• 160 posti utensile
• Sistema di pulizia del porta utensili
• 1 operatore richiesto
• Scarico SB (Scarico Bancale)
• IMML (opzionale)
• Spazio 16,4 metri x 7,5 metri
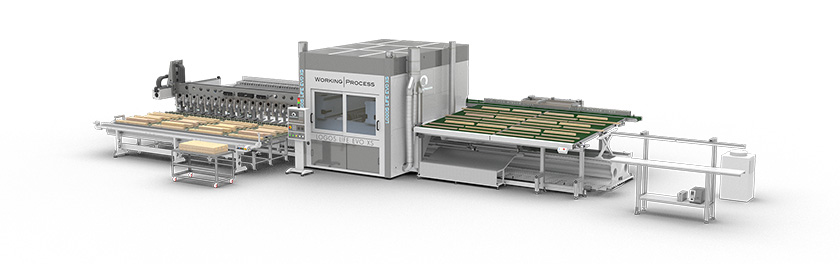
Logos Life EvO XS: 2253 BB SB
Linea di produzione per finestre CNC multi-mandrino con caricamento manuale del pezzo e scarico automatico, 2 portali con 2 mandrini di fresatura, 8/10 morse completamente indipendenti e 160 posti utensile, garantendo massima flessibilità e produttività.
• 2 motori mandrino T5/T5c
• 8/10 morse indipendenti
• 160 posti utensile
• Sistema di pulizia del porta utensili
• 1 operatore necessario
• Scarico SB (Scarico Bancale)
• IMML (opzionale)
• Dimensioni 16,4 metri x 7,5 metri
• 2 motori mandrino T5/T5c
• 8/10 morse indipendenti
• 160 posti utensile
• Sistema di pulizia del porta utensili
• 1 operatore necessario
• Scarico SB (Scarico Bancale)
• IMML (opzionale)
• Dimensioni 16,4 metri x 7,5 metri
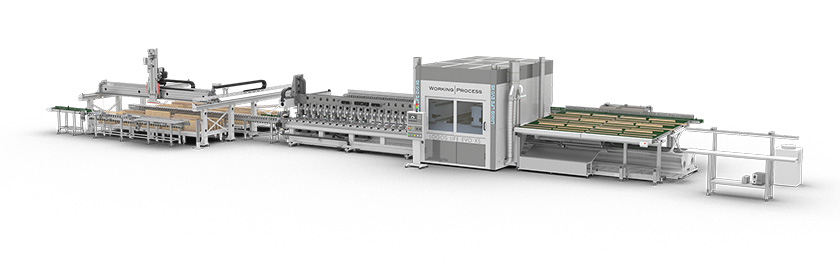
Logos Life EvO XS: 2353 IMML SB
Linea di produzione per finestre CNC multi-mandrino con caricamento manuale del pezzo e scarico automatico, 2 portali con 3 mandrini di fresatura, 10 morse completamente indipendenti e 160 posti utensile, garantendo massima flessibilità e produttività.
• 3 motori mandrino T5/T5c/T5
• 10 morse indipendenti
• 160 posti utensile
• Sistema di pulizia del porta utensili
• 1 operatore necessario
• Scarico SB (Scarico Bancale)
• IMML (opzionale)
• Dimensione 17,4 metri x 7,5 metri
• 3 motori mandrino T5/T5c/T5
• 10 morse indipendenti
• 160 posti utensile
• Sistema di pulizia del porta utensili
• 1 operatore necessario
• Scarico SB (Scarico Bancale)
• IMML (opzionale)
• Dimensione 17,4 metri x 7,5 metri
Specifiche Tecniche
Logos Life EvO XS 2353 BB SB
Sistema Operativo
SIEMENS 840D SL
Dimensioni di lavoro dei pezzi (grezzi in ingresso)
Altezza: Min 20mm – Max 150mm
Larghezza: Min 40mm – Max 300mm
Lunghezza: Min 230mm – Max 6300mm
Potenza elettromandrni installati
S1 19Kw
S6 25Kw
Asse C di posizionamento
360°
Attacco utensile
HSK- 63E
Peso massimo utensile
15Kg
Diametro massimo utensile
280mm
Lunghezza massima albero
260mm
Magazzino utensile
130/190 postazioni
Sensori rilevamento pezzo
Altezza
Lunghezza
Larghezza
Serrande aspirazione
Numero di serrande controllate in base al modello.