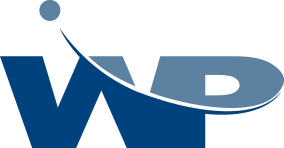
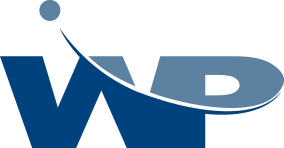
Logos Life EVO XS
Maximum wooden window production with minimum footprint!
Compact, fully automatic work center for the production of wooden windows and doors of any shape and size. It features automatic loading and unloading, a dual-grip manipulator, and a monoblock structure with 2 or 3 milling spindles. It has 8 fully independent workpiece-holding clamps and 128 tool places, ensuring maximum flexibility and productivity. It can be integrated with intelligent loading and unloading systems.
Ideal for producing 10 to 25 windows per day!
Loading System
The BB and IMML loading system is optimized for loading rows of pieces, maximizing available space, and enabling variable positioning of the pieces.
This fully automated system can load between 1 to 10 pieces simultaneously, ensuring their optimal clamping in the grips and enabling machining on all 6 faces. Additionally, it offers dimensional verification of incoming elements, optimization of piece arrangement in rows, load preparation, and management of pieces with different widths.
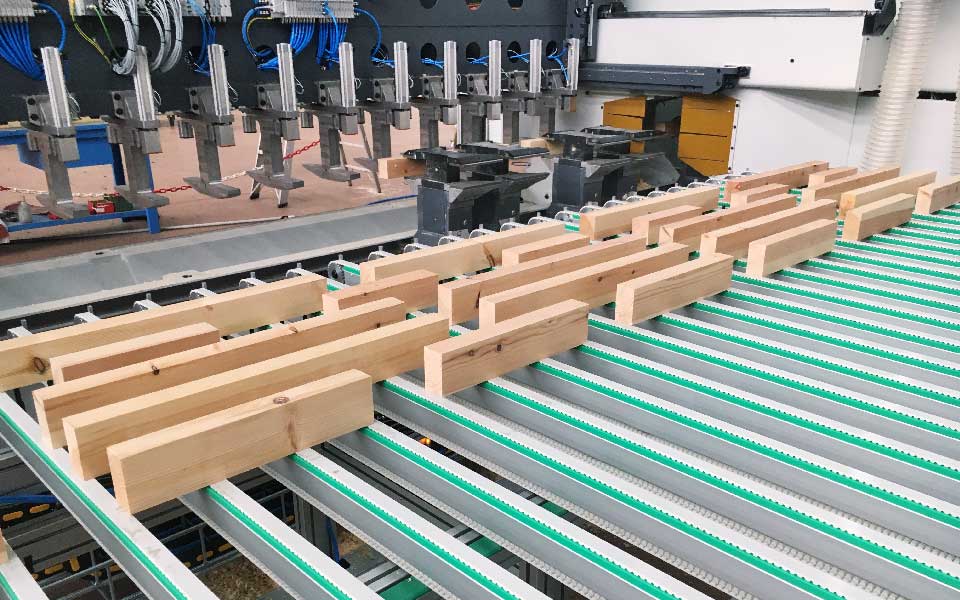
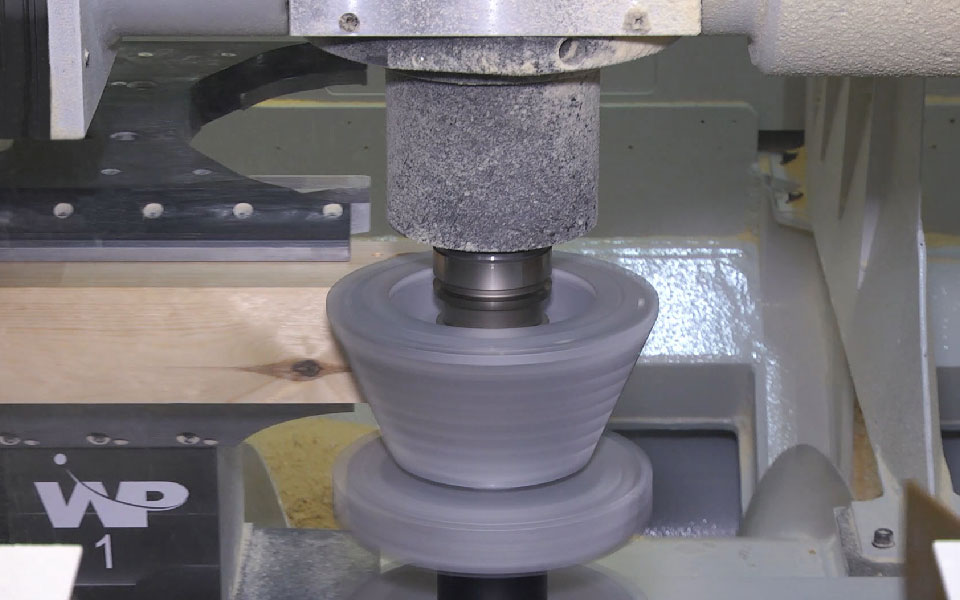
Transport Clamps
The double workpiece clamping clamps are designed with pneumatic closure and independent motorized longitudinal translation. Their size and shape have been optimized to ensure the best accessibility of tools to the workpiece during processing.
These clamps are managed as independent interpolation axes, offering additional flexibility that results in increased overall production capacity. The clamps are characterized by flexibility, robustness, and adaptability, with pressure adjustment according to specific processing needs and optimal positioning on the wood to ensure an effective and high-quality grip.
Each clamp is designed to be independent, with the ability to adjust the gripping pressure, reposition infinitely without compromising precision. Additionally, they are equipped with adaptable features, such as micro-needles, to handle different work phases and anticipate future processes.
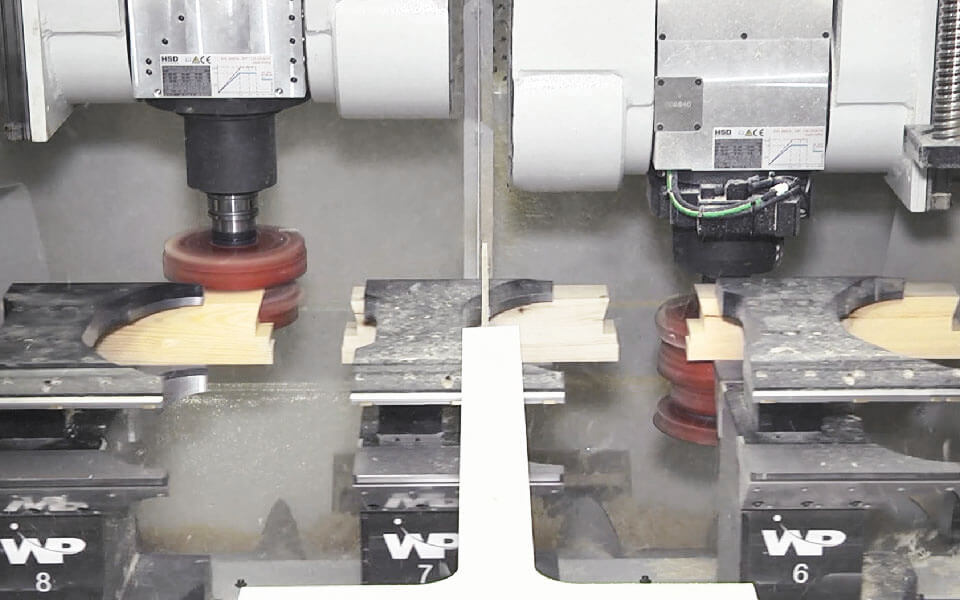
Operating Heads
The T1, T5, and TBR operating heads represent the result of 20 years of research and development. For example, the double lateral clamping systems of the T5 heads, even with integrated C-axis, offer flexibility and precision in tool positioning.
This ensures optimal cutting conditions, reducing stress on the electrospindle.
Tool Magazine
The Tool Magazine is designed as a rack system with an electro-welded steel structure and with longitudinal sliding movement on guides with ball-bearing carriages.
The system allows simultaneous tool change operations on all spindles, reducing idle times and consequently increasing productivity.
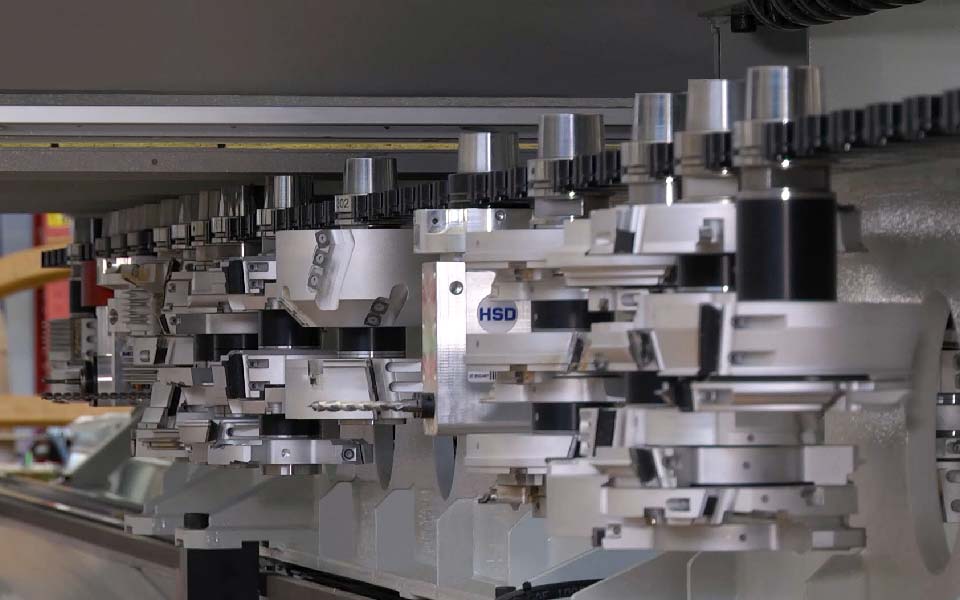
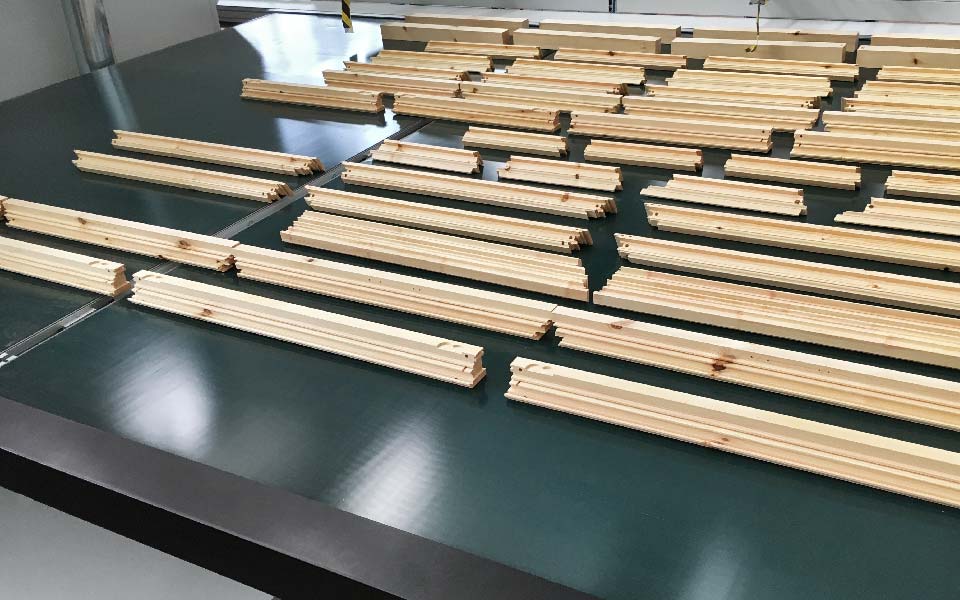
Unloading System
The proposed unloading system is highly customizable and modular, designed to ensure optimal efficiency in logistics management. Its ability to maintain a predefined work sequence ensures accurate synchronization during the unloading process, guaranteeing a seamless workflow and optimal resource utilization.
A key feature of this system is its extended operational autonomy, ranging from a minimum of 1 hour up to 3 continuous shifts (UML). This characteristic offers significant operational flexibility, minimizing downtime and allowing for continuous operations management.
The system efficiently performs unloading operations, including advanced quality controls to ensure compliance with standards. Additionally, it integrates an automatic labeling process at the end of unloading operations, simplifying material management and improving traceability.
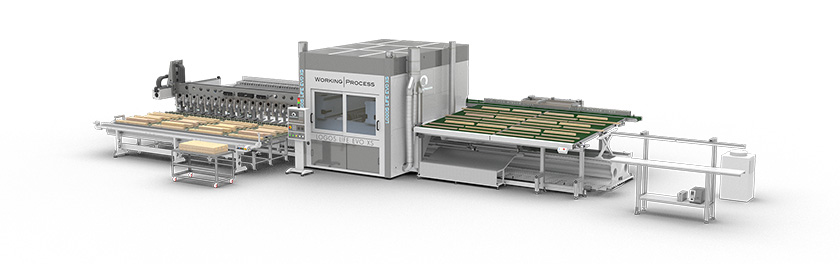
Logos Life EvO XS: 2253 BB SB
CNC window production line with manual workpiece loading and automatic unloading, 2 portals with 2 milling spindles, 8/10 fully independent workpiece-holding clamps, and 160 tool places, ensuring maximum flexibility and productivity.
• 2 spindle motors T5/T5c
• 8/10 independent clamps
• 160 tool rack
• Tool holder cleaning system
• 1 operator required
• SB unloading (SB = Pallet Unloading)
• IMML (optional)
• Space 16.4 meters x 7.5 meters
• 2 spindle motors T5/T5c
• 8/10 independent clamps
• 160 tool rack
• Tool holder cleaning system
• 1 operator required
• SB unloading (SB = Pallet Unloading)
• IMML (optional)
• Space 16.4 meters x 7.5 meters
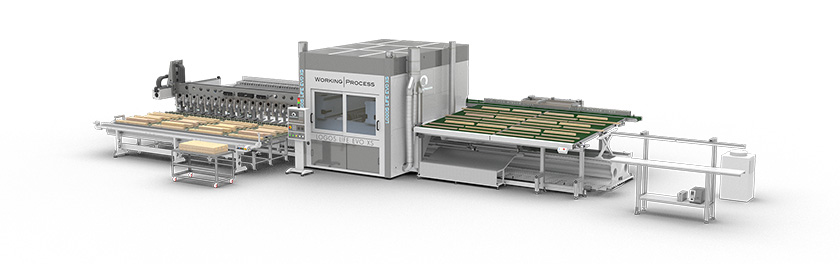
Logos Life EvO XS: 2253 BB SB
CNC window production line with manual workpiece loading and automatic unloading, 2 portals with 2 milling spindles, 8/10 fully independent workpiece-holding clamps, and 160 tool places, ensuring maximum flexibility and productivity.
• 2 spindle motors T5/T5c
• 8/10 independent clamps
• 160 tool rack
• Tool holder cleaning system
• 1 operator required
• SB unloading (SB = Pallet Unloading)
• IMML (optional)
• Space 16.4 meters x 7.5 meters
• 2 spindle motors T5/T5c
• 8/10 independent clamps
• 160 tool rack
• Tool holder cleaning system
• 1 operator required
• SB unloading (SB = Pallet Unloading)
• IMML (optional)
• Space 16.4 meters x 7.5 meters
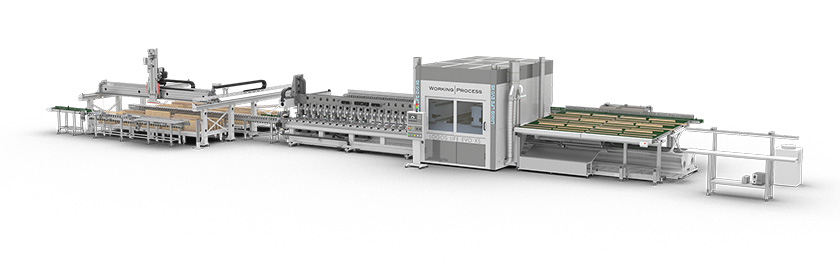
Logos Life EvO XS: 2353 IMML SB
CNC window production line with manual workpiece loading and automatic unloading, 2 portals with 3 milling spindles, 10 fully independent workpiece-holding clamps, and 160 tool places, ensuring maximum flexibility and productivity.
• 3 spindle motors T5/T5c/T5
• 10 independent clamps
• 160 tool rack
• Tool holder cleaning system
• 1 operator required
• SB unloading (Pallet Unloading)
• IMML (optional)
• Space 17.4 meters x 7.5 meters
• 3 spindle motors T5/T5c/T5
• 10 independent clamps
• 160 tool rack
• Tool holder cleaning system
• 1 operator required
• SB unloading (Pallet Unloading)
• IMML (optional)
• Space 17.4 meters x 7.5 meters
Technical Specifications
Logos Life EvO XS 2353 BB SB
Operating System
SIEMENS 840D SL
Workpiece dimensions (raw material input)
Height: Min 20mm – Max 150mm
Width: Min 40mm – Max 300mm
Length: Min 230mm – Max 6300mm
Installed electrospindle power
S1 19Kw
S6 25Kw
C-axis positioning
360°
Tool holder
HSK- 63E
Maximum tool weight
15Kg
Maximum tool diameter
280mm
Maximum arbor length
260mm
Tool magazine
130/190 positions
Workpiece detection sensors
Height
Length
Width
Suction shutters
Number of shutters controlled depending on the model.