At B.G Legno, investments in technology are considered the condition for being “on par” on the market and for standing out with a contemporary product. When all the main aspects of the business are shared within a precise strategy, it is possible to develop a process to give shape to a project and provide concrete arguments to the showroom. The partners of this investment are considered indispensable by Samuel Olla who tells us about a company from the Pistoia area that is successful in many respects. On November 12th in Campo Tizzoro, where B.G Legno is located, Pietro Ferrari, editor of Web and Magazine, Tiziano Innocenti of Oma, Paolo Perservati and Filippo Schegginetti of Working Process sit around the work table.
IN THE OFFICE «Our investment was dictated by the change taking place in the wood, wood-aluminium and wood-glass window and door sector – begins Samuel olla –, to create innovative products to the point of being different from everything else the rest of the national competition, because we operate on the regional market but also throughout Italy. We need to give our showrooms concrete arguments and to have them we aimed to have innovative products.”
What was the biggest difficulty? «Our difficulty was developing the entire process, the company works to produce the window with individual pieces. It is a window of which every single component goes through production from start to finish, then the “puzzle” of the pieces is created and everything is assembled through mechanical fixing, then the glass is mounted inside the window: this is a very new concept , at least as we conceive it. This procedure already existed, but it used an adhesive tape mounted from the inside, whereas here the objective is the quality of the product. Another element to emphasize is that ours is a window without glazing bead, which not only involves a difficulty at the production level, but also for the suitable supplier because a glazier must work on 1/2 mm of thickness, a tolerance that implies a glass factory of great professionalism and reliability, only possible with the craftsman – industry, because the industry does not personalize the glass and the craftsman does not have the means and therefore has standardized the product”.
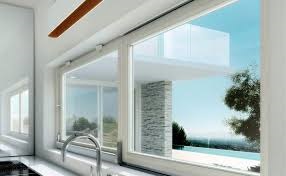
What is the story of B.G Legno? «It is a company that was founded in the 1950s as a small carpentry shop, it served the industrial complex of Campo Tizzoro, in the province of Pistoia, where we are located, where 6000 people worked and therefore B.G carried out industrial maintenance and packaging. The owner was an elderly person and in ’94 the company was taken over by two partners: Bragalli and Galeotti, then in 2004 I joined with my father and other partners – subsequently liquidated -, and until 2008 I gained technical experience in production . In 2014 the company became part of the Olla family.”
How is it structured today? «Today we are 30 internal people, we have 10 agents, two hired commercial figures and a series of professionals – belonging to an independent studio – who follow the communication part, carrying it forward with quality and continuity. Recently we have entered Treedom (www.treedom.net), a web platform that allows you to plant a tree remotely and follow it online, with the intention of giving each customer a coupon demonstrating the purchase of a tree and the replenishment of CO2 to which it contributed. A choice consistent with our FSC and PEFC certified products, but which also allows us to choose wood; in fact, for example, for a wood – aluminum product with a wide glazing bead, unlike our competitors we do not use the standard laminate, but an ad hoc product in 3 layers all in the entire list defined as DDD, so that even on wood – aluminum the three layers are never joined. It is as if it were an extrusion of wood, a piece where there is nothing manually applied, this is an evolution but the problem is that the material cannot be found, so we request custom-made pieces. A difficulty never faced before in any other project, also because there are serious and less serious suppliers, others who delay. Following the complete reindustrialization of the processes, last year’s turnover remained almost stationary, this year’s turnover showed a 45% increase in turnover already in September, from around May the trend showed a growth of 40 to 55% more on the month so this is good data.
This result is due to a series of commercial choices. Starting from the consideration that the 20,000 euro per year retailer has become a cost for a company, it was decided to take the most important retailers and with them create a store project, therefore a store loyalty in which to make a single-brand sale , while the customer decides where to buy the doors or other surrounding elements. The important thing was to open up the possibility of making direct invoicing with these showrooms, so the product is not sold off and direct sales can also be made, this has led to a drastic increase in turnover. Internally we have a technical office that gives the answers, a customer service that notifies the user. It is a service that costs money, but the sales process must be followed as the product is complex and must be well explained to avoid problems. Our marketing office conveys the product and offers this type of service to the customer, and, truly innovative, also a credit purchase service – if we work with important companies – which allows us to pay our reseller the advance commission and allows us to stay calm about the proceeds”.
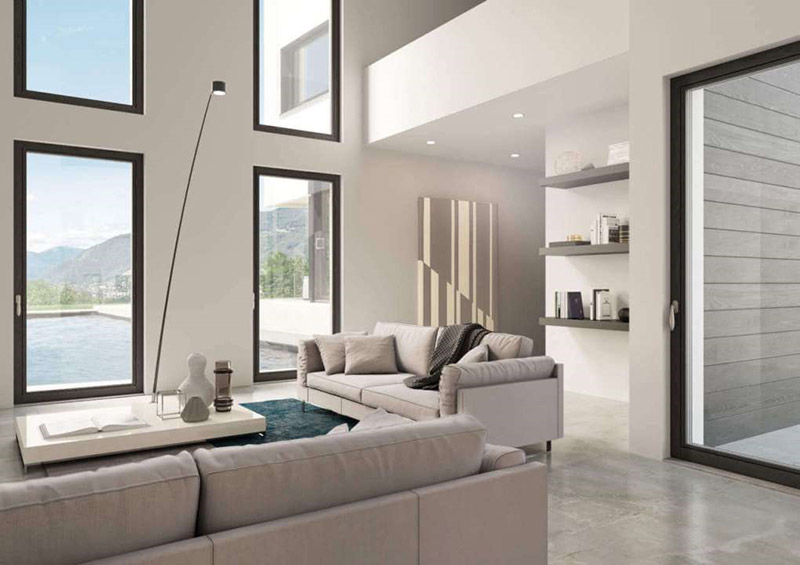
This strong product specialization has proven successful! «Yes, it works because synergy is created, all figures are involved from production to sales and this investment pays off. In fact, it is a large project, here in Campo Tizzoro there is the production headquarters, but then there will be the opening of a direct store in Prato, in Florence there is another store, as in Arezzo, Rome, Milan , Lecco and Cesena, and there will be another one in Bologna, then there will also be one in Puglia. We don’t even abandon the 40/45 customers who turn to us, following them directly from the company, because they are the smallest ones but they have also contributed to our investment and the growth of the company; However, everyone must be followed because ours is a difficult product.”
B.G Legno’s strategies are now defined: how are responsibilities divided? «I have always pursued them but it took time to give them shape and I have very well-trained collaborators around me: the technical sales manager Davide Piliero, the sales director Francesco Buccafurni, the technical design manager Michele Finocchi, every order goes through him who orders particular materials from suppliers, manages the entire cycle of putting the orders into production and the generations for the various plants, he is a fundamental figure. Then there is the customer service manager Roberta Filoni, we provide a service so there is no need for the telephone, which rarely rings, because everything is already programmed. It’s been like this for 7/8 months, but it wasn’t like this once, more people were needed in the call center, risking giving even less service. Now, we have reached a good level of efficiency.”
It is essential to transmit such a new product which then represents the heart of the entrepreneurial project! «It all comes from an analysis of the market which led us to minimal products and strong innovation, which first of all in the production phase does not require us to get our hands on the product, conceived as an extruded PVC or aluminum but made with wood. We started working on this at the end of 2017, myself, Michele Finocchi and my father, responsible for the entire production department, who also presides over the work of DDX while transmitting the data into production. In fact, it is Logico and DDX that talk to each other for the generation of the product: the consequential transition takes place from Logico to DDX to the machine that receives all this data which becomes the design and the product”.
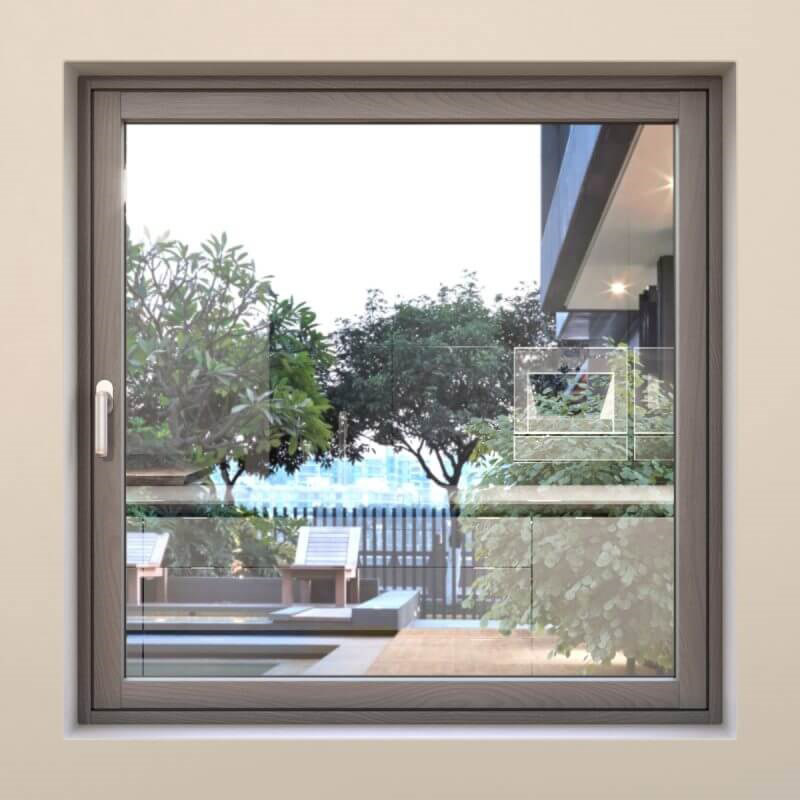
We ask Paolo Perservati how the work center communicates with the program.
«The machine/program connection is total and completely integrated. The system receives the work list and processes the requested pieces in total safety thanks to the collision control previously verified with DDX, guaranteeing total verification of the work operations thanks to the WWLine supervisor developed by Working Process. This is a production technology that guarantees the release of the material in predictable and certain times, without the operator having to intervene. One of our objectives has always been to give freedom of choice to those who have to produce windows, to be able to design a product, as in the case of B.G Legno, which did not exist before, going beyond limits and conventions. Finally form follows function, without compromise, for total freedom of technical and aesthetic thought in the window world”.
You both put the window in the center, this led to a futuristic project! «Yes, very innovative and with enormous difficulties – continues Samuel Olla –, not at the level of systems but inherent to problems of marking the pieces, because working horizontally there was a problem linked to the assembly line, so the benches were changed four times in three months and in the meantime we had to produce! This had me a little disheartened because I saw that there was demand and my fear was that I wouldn’t be able to develop the commercial area because I didn’t have the right tools: I wasn’t worried about production but about the commercial aspect.”
Of course it is a great responsibility and perhaps the crisis has influenced certain choices… «In 2007 we were small and it was our fortune to have a solid and healthy company that allowed us to grow. Clearly you need to find support in the financial system and you need people who follow you and find ways – not too heavy – to dilute investments. Commitment is obviously necessary, but those who provide you with a certain amount of support from behind are also important. It was a big responsibility and a risk for us, both for all the people who work here and for all the investments made. The great satisfaction came with the response that is arriving, and even if there is still a lot to do, this is what counts.”
What is your view on the market? «For now, as anticipated at the beginning of our meeting, it is mainly an Italian market, in Switzerland we are working but marginally, but I hope there will be a positive development in Dubai, because in November we will participate in the Big 5 in Dubai, a important construction fair for the Middle East, Asia and Africa, and I hope there will be an important outlet.” In Italy? «In Italy, the high-end market is interesting, where a 360° service must be given, from the design of the window hole, to the construction site, to the company’s technicians on site for taking measurements, to the design of the casing and the 3D drawing! A type of construction site in which BIM is used, so the customer has a precise perception of the product and when a customer spends a lot on windows – as for any other durable product of the property – he expects something done well. This is the market today, and it is a difficult market because you are fighting to maintain production numbers while operating in a high target range and matching these two elements is not easy.”
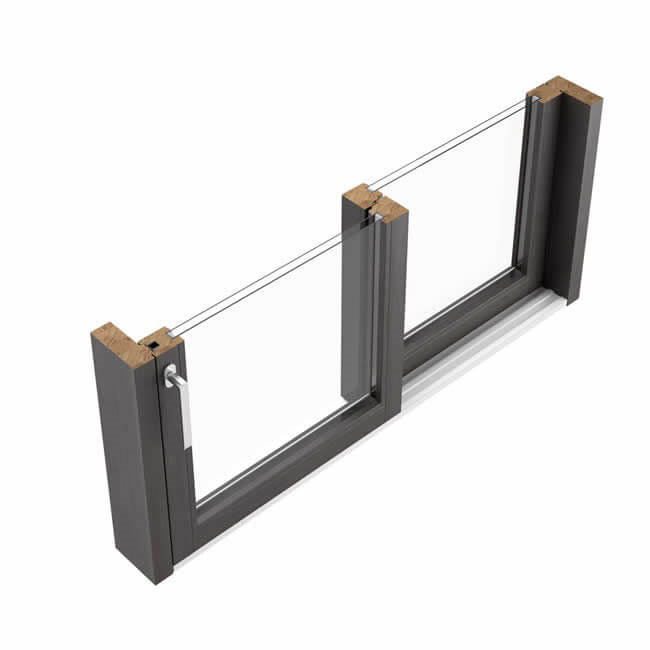
Filippo Schegginetti highlights the reference to BIM, to the importance of coordinating everything around the house and then brings it back to the client and asks if there is also an intermediate figure, such as an architect, who coordinates these aspects. «The main difficulty for this company now is identifying the target, because you can go anywhere on the market and before having established yourself, because I don’t have the presumption of saying that we have already established ourselves, it is difficult to distinguish between a construction site and the another because the mentality can be the opposite and reserve surprises – not always positive ones. Certainly, working with quality and targeting professionals has led us to word of mouth that is consistent with our way of operating, but it is difficult to always be certain of the caliber of our interlocutor, which is why having a reference professional is a great help, always desirable. ».
In the catalog we read “Superior quality windows and doors” referring to wood and wood-aluminium, and in front of us we have the corner of a “minimal”: we are talking about performance. «The performances are excellent, the values are significantly lowered because the glass makes the difference, and the wood in any case is intrinsically high-performance. With the integrated glazing bead, a source of weakness towards infiltration or break-ins is eliminated to create a truly safe and durable frame. A variable of all the products is what we call a renovation frame, a single body composed of both the frame and the architrave: a finishing without additional elements”.
What variations of wood species do you use? «Laminated pine, oak, larch, ash, fir and okùme, the latter is out of line, but it can be done. However, the main woods are pine, oak and laminated larch because they represent a compromise between pine, a soft wood which therefore guarantees maximum thermal insulation, and oak which is required especially in the central south, where the thermal values are different and there is a dissimilar culture of the house which prefers wood with more substance and more compactness. In the north they are more concrete, for example in Milan they choose pine for the interior and aluminum cladding for the exterior. Even the paint has a particular cycle, the Rennerstandard cycle is not used, but the Top Quality, which allows you to obtain the guarantee from 7 to 15 years, but the real guarantee is the loose piece, because every single component is painted and assembled after, so the paint adheres to every part of the product. We are exclusive in this type of painting, both because it requires a very complex management system and because it requires an innovative assembly system that can only be achieved with specific procedures.”
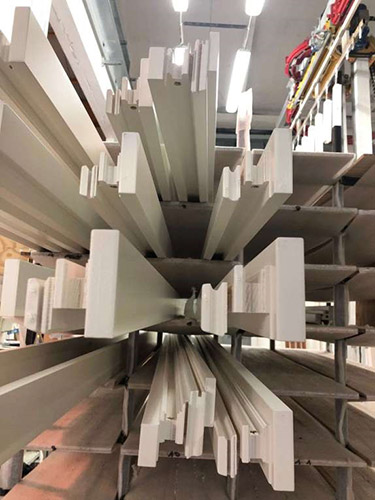
IN PRODUCTION Samuel olla illustrates the production department with Paolo Perservati, Filippo Schegginetti and Tiziano Innocenti. «We have small just in time wood warehouses – which he tells us – for what is needed during the day and therefore they are rearranged daily, they are closed and divided by wood species: softwoods and hardwoods. Moving on to the production layout, a union of orders, optimized at the end of the machine, enters the Salvador plant for cutting, i.e. initially the semi-finished products are placed randomly, divided only on the basis of thickness and are subsequently perfected by dividing the orders by cart. Then the SCM planer brings the piece to the required thickness, through multiple planers that work on the 4 faces, the product which from raw becomes planed; subsequently the “tunnel” wets the product: we make two wetting paths, one here and the other with a machine that is used to simulate a painting path before this is carried out, in order to prepare the piece for treatment. At this point the orders are already divided and after calibration they enter the corridor of the Working Process machining centre, they go to the warehouse which carries out an analysis of width, length and height. If it goes well, the material is introduced into the production process, otherwise it is discarded. in this green area – which is shown to us – but it never stops. Here, to optimize production, all the pieces are placed by type, not by type of product but by type of processing. Thanks to the programming divided by essence, the system manages the advancement speeds: with soft woods it works up to 18 metres, with hard ones up to 14 metres, then the process continues and the material passes to another area… it’s as if they were 5 machines together working in synergy: loading, load management, grippers, production and unloading. The beauty of the system is that during the processing steps and changes it carries out other operations, for example while positioning the grippers from one part of the piece to the other, at the same time it also prepares the other products, so it is truly a continuous process ».
Does the Working Process work center require the presence of an operator? «The machine guarantees unmanned operation – Paolo replies
Preserved – and for a certain time the operator can carry out other operations, it means that the machine can still work autonomously”.
Then we move to the painting department: are the windows and doors painted individually and then assembled? «Yes, exactly, here there is the double Cefla painting system – replies Samuel Olla –, one concerns the color part which works in the bin and not in the tub in order to have maximum production flexibility, the other is that of the intermediate. You can see how the finishing cycle is carried out with 4 coats: primer, intermediate, primer and finish. Here it is also highlighted how the 3 layers of the lamella cannot be seen in the finished product because the lamella is composed in thickness, so a greater thickness of the lamella is never displayed. It means never seeing the stratification of the slats on the element which thus appears to be a single solid piece; but the innovations we have introduced are many: from the single piece of the architrave – frame, to the tenon with double mechanical fixing, and this is really quite innovative. And then there is the concept of minimalism which with the machining center allows you to work on 52 mm without having problems: the Working Process is useless if you are not innovative! Going back to the description of the painting process, after the primer, the elements are detached and sanded
with a brush. This step precedes quality control, but at this stage it already allows you to verify the result. The finish is flawless! The second Cefla plant was purchased in 2017/2018, alongside IGiotto, following the update of the production layout dictated by the purchase of the Working Process machining center which changed “the numbers” and to adapt we had to implement all the technology to bring it to the same speed. Of course it’s not just about speed but thanks to the work center total flexibility. Take for example this 70 mm window profile, each line has 5 profiles: rounded, squared, slightly rounded, diamond and rustic, this one in particular is diamond. But if you wanted to create the interior and exterior in two different ways, since the cutters are mounted on independent working heads, you could differentiate the profiles on the two sides of the window, for example making the interior square and the exterior rustic. . This is precisely thanks to the flexibility of the cutters, another added value: they are, in fact, two different cutters that work on two different spindles and having dedicated tools allow the internal part to be profiled with one profile and the external part with another”.
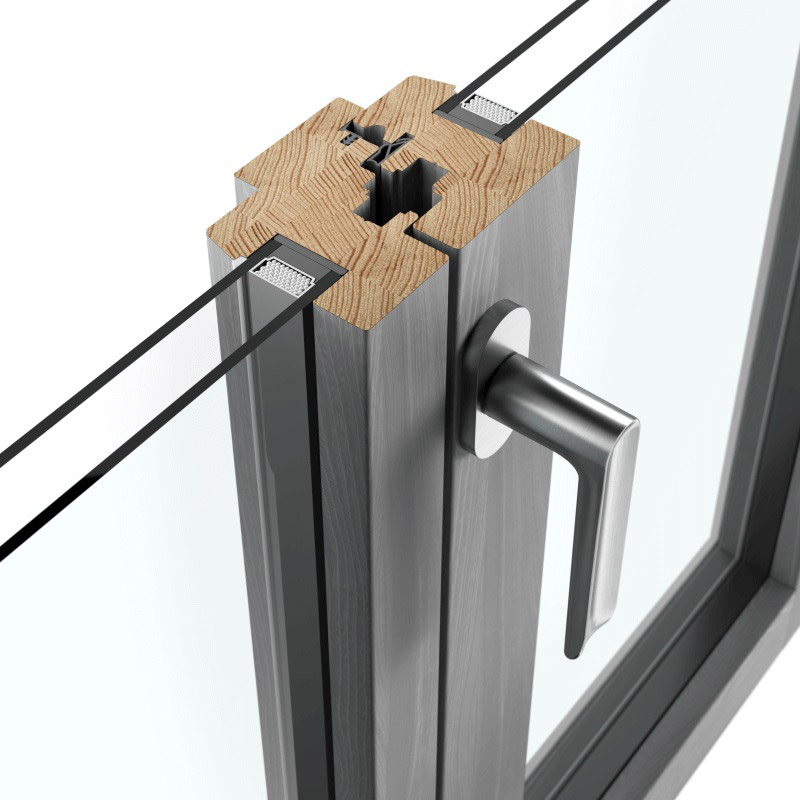
The painting department has therefore been automated to bring it up to the speed of the Working Process work centre: now there are no more trolleys waiting? «Yes, now everything works, on the one hand the system does the primer and works on all the heads, the advantage is that it also paints from the front, and once the process is completed the quality of the product is totally different; the robot operates on the other side. The difficulty lies in controlling the thickness of the paint, because the rough one is not like the finished one, so it is essential that the cutter smooths all the parts uniformly. Another very important aspect is that once the work is finished, the robot cleans itself automatically, and particularly in summer when it is hot and residues remain on the pieces, cleaning is essential. Drying occurs naturally in the tunnel in approximately 2 hours of drying.”
Is a protocol followed for each order? «A meeting is organized between the managers of the various departments before going into production, in order to analyze the particularities of the order. In this department there is quality control of all the orders that travel along a corridor, and all the pieces, one by one, are taken and checked manually: the lamps are used to avoid tiring the eyes. Observing the connection between uprights and transoms, the double junction with the mechanical fixing and the tenon, which is in turn divided into different types, is highlighted. It is, in fact, a double tenon on the door which is not the traditional comb tenon, but is a full interlocking tenon with an anti-torsion tooth (to avoid movement of the piece) which is inserted between the upright and the transom in a very innovative, and also on the frame the tenon is double: the toothed tenon is joined to another round tenon which allows us to increase the performance on the joint, because when the wood swells, it has the possibility of settling naturally, while the classic square tends to split. In short, we have taken all the good features of the existing systems and customized them: the mechanical fixing without glue instead of the counter-shaped pins that swell and the tenon to guarantee durability and stability to the frame and at the same time we give aesthetics and harmony to the final product”.
We cannot leave production without meeting Marco olla, to whom we ask what was the most complex moment of this project to create a new window and door! «The most difficult thing was to train the staff with this mentality and therefore a new approach, then they got motivated, but initially it was difficult with this completely new system which mainly involved removing the glue by playing on the double joint. In this way you can do what you want a little more, clearly with gluing we were more limited, and the difference to highlight is the duration over time: since we produced it this way, we have no longer received a phone call from a customer who wanted to express problems. The effort was enormous, both in forming the team but also in finding new solutions: it was very challenging but extremely rewarding.”
IN THE SHOWROOM – HARDWARE AND PACKAGING DEPARTMENT We then move to another warehouse, where the windows are ironed and packaged, and whose mezzanine is occupied by the large showroom and the conference room. «The truck arrives from the production shed that we have just visited, with the material that has already undergone quality control, and there is also a part linked to extra production such as the lift-and-slide ones. Here the individual pieces are assembled, therefore from the disassembled piece to the finished piece, which are then divided into trolleys to be shod: wood and wood – aluminum are divided into two different paths because the latter is assembled and shod before assembling the aluminium. , while in wood the glass is mounted on dedicated suspended benches given the absence of the glass bead. The bench is used suspended when the glass must be raised to mount it around the window, or lying down when used as a support surface. Here there is the wood – aluminium, further on the hardware part. The hardware bench also follows the same principle: do not run around the window, but rotate the window. In this sector it is possible to see the entire line, the frames travel separately from the doors but then join together. Another added value of the Working Process that I would like to underline is the low arch window without glass bead, this is all machine made and the glass is inserted into the already prepared groove. The packaging is also automatic – every single window is packed in the machine -, our logistics includes labeling and the crate is pre-designed and arrives together with the order to be carried out. In a department adjacent to the packaging, the crates are made, in 4 more or less standard sizes, for each order.”
And what are the handles attached to each window for? «The handles are used to package the window and above all so that the customer can take it on site, and the underlying fir strip so that the lower crosspiece of the window does not get damaged when it is placed on the ground. And once mounted, according to the type of products, a small piece is inserted as a spacer between the windows. These are all precautions aimed at preserving the integrity of the product.”
The pose? «The installation is carried out by us as regards the direct work, then there are the stores and retailers who also organize the installation».
In the vast Showroom we focus on B.out, a wood-aluminium window and door. «This window was born from Working Process: B.Out gives the feeling of being outside but inside the house, because it seems like being outside given the essentiality of the profile of the window».
Then we look at a minimal: can’t we obtain the symmetry in the central node having to receive the handle? «The profile that receives the handle is 3 and a half centimeters wide, there is a product that I designed to answer this question which is a wooden window and door and is called Cloud, a symmetrical but non-invasive and decidedly minimal product».
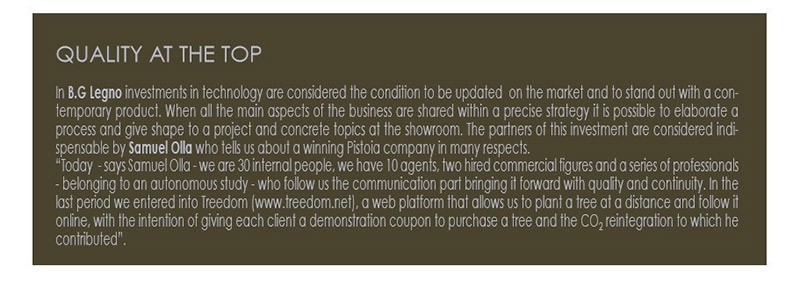